Build to Print Manufacturing Meets Tooling Engineering: Precision for Aerospace Product Development
Discover how build to print manufacturing and tooling engineering work together to deliver precision in aerospace product development. Learn how this combination ensures accuracy, efficiency, and quality in advanced aircraft components.
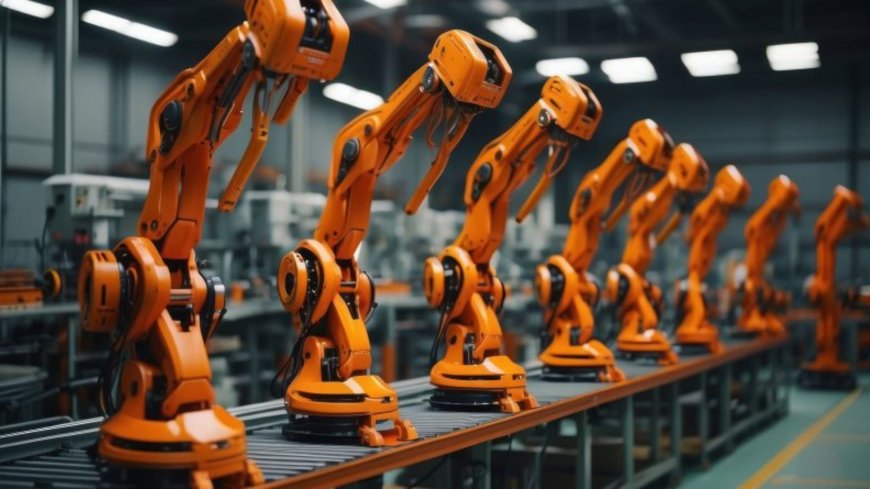
Aerospace product development requires high levels of precision, efficiency, and quality. As the demand for lighter, stronger, and safer aircraft components grows, manufacturers are turning to advanced processes that reduce errors and increase performance. One of the most reliable approaches involves the combination of build to print manufacturing and tooling engineering. Together, these two methods ensure that complex aerospace components are built exactly to specification while meeting strict industry standards.
This collaboration supports every stage of the aerospace development process—from prototyping to full-scale production—allowing engineers and manufacturers to deliver accurate and consistent results.
What is Build to Print Manufacturing?
Build to print manufacturing is a process where the manufacturer produces a part or assembly based on exact customer-supplied designs and documentation. These technical drawings include all required dimensions, materials, tolerances, and finishing standards.
Unlike design-to-build methods, where the manufacturer helps create the design, build to print focuses entirely on executing what is already planned.
Core elements of build to print manufacturing:
-
Strict adherence to customer drawings
-
Detailed documentation and revision control
-
Use of certified materials and equipment
-
Quality control procedures to meet aerospace standards
Because accuracy and compliance are non-negotiable in aerospace, this method allows companies to ensure uniformity, reduce waste, and speed up production timelines.
The Role of Tooling Engineering in Aerospace
Tooling engineering involves the design and development of the tools, jigs, dies, fixtures, and molds needed to build a part or structure. In aerospace, tooling is crucial for supporting repeatable manufacturing processes, especially when tolerances are tight and components are highly complex.
Tooling engineers create the foundation for accurate part production. Their designs help operators align, measure, and fabricate parts with minimal variation.
Typical tools used in aerospace manufacturing:
-
Assembly fixtures for precise part alignment
-
Trimming tools for composite materials
-
Drilling jigs for accurate hole placement
-
Forming dies for sheet metal shaping
-
Bonding tools for high-strength joins
These tools must be designed to last through repeated use while maintaining dimensional accuracy throughout.
Why Precision Matters in Aerospace
Aerospace systems operate under extreme conditions. Every part must meet exact performance requirements because even a small error can lead to major failures. Whether it’s a component for a commercial jet or a spacecraft, consistency in production ensures safety, reliability, and performance.
When build to print manufacturing is paired with expert tooling engineering, it becomes possible to deliver that level of precision at scale.
Benefits of precision in aerospace:
-
Reduced risk of in-flight failure
-
Better fuel efficiency due to optimized parts
-
Shorter assembly times from accurate fitment
-
Lower maintenance costs from higher durability
These benefits are essential for meeting the expectations of aerospace clients, airlines, and regulatory bodies.
How Build to Print and Tooling Engineering Work Together
The strength of this manufacturing approach lies in the close relationship between the design files and the physical tools used to build each part. Tooling engineers use the original prints to create jigs and fixtures that make production repeatable and efficient.
Step-by-step collaboration:
-
Customer provides the drawings and specifications.
-
Tooling engineers design the necessary production tools.
-
Tools are built and validated for accuracy.
-
Manufacturing teams use these tools to produce parts exactly as required.
-
Quality control teams inspect finished parts to ensure compliance.
This streamlined workflow minimizes errors and ensures all parts meet the same high standard every time.
Challenges in Aerospace Product Development
Even with precise tools and clear documentation, challenges can arise. Aerospace projects often involve short lead times, high complexity, and continuous design updates. Managing these changes without affecting part quality requires coordination across teams.
Common issues include:
-
Tool wear or misalignment over time
-
Late-stage design modifications from clients
-
Delays in material sourcing or certification
-
Integration of new technologies like additive manufacturing
To manage these challenges, companies need experienced tooling engineers and flexible manufacturing systems that can adapt without sacrificing quality.
Quality Assurance and Compliance
One of the strongest advantages of build to print manufacturing combined with tooling engineering is the ease of quality assurance. Every part is built to a specific print, making it easier to check dimensions, finishes, and material standards.
Using standardized tools and processes also simplifies audits and regulatory reviews, which are frequent in aerospace environments.
Quality steps often include:
-
First article inspection (FAI)
-
In-process measurements and checks
-
Final inspection with digital documentation
-
Traceability of tools, materials, and processes
This level of control builds trust with aerospace clients and meets the strict requirements set by international aviation authorities.
Applications Across Aerospace Sectors
The partnership between build to print manufacturing and tooling engineering supports a wide range of aerospace products.
Common applications:
-
Wing structures and control surfaces
-
Engine mounts and housings
-
Interior components like seating frames and tray tables
-
Satellites and spacecraft assemblies
-
Drone airframes and landing gear systems
By maintaining accuracy and speed, this combination supports both large-scale production and one-off custom aerospace builds.
Conclusion
Precision and performance are the pillars of aerospace product development. When build to print manufacturing joins forces with tooling engineering, companies gain the ability to create high-quality, complex parts consistently and efficiently. This powerful partnership helps the aerospace industry meet increasing demands for safety, efficiency, and innovation.
By focusing on collaboration, accuracy, and quality control, manufacturers can deliver parts that perform flawlessly in the air, in space, and beyond. As the aerospace industry continues to evolve, the value of combining detailed prints with smart tooling will only grow—ensuring that the future of flight remains strong, safe, and precise.